A business is only as good as the products it offers. If the quality of your products falls short, your customers are going to look for alternatives.
Poor-quality products can cost you more than sales. They can also cost your business’s reputation. So how can you make sure your products make the grade? In part one of this article, we look at why quality control is important for your business.
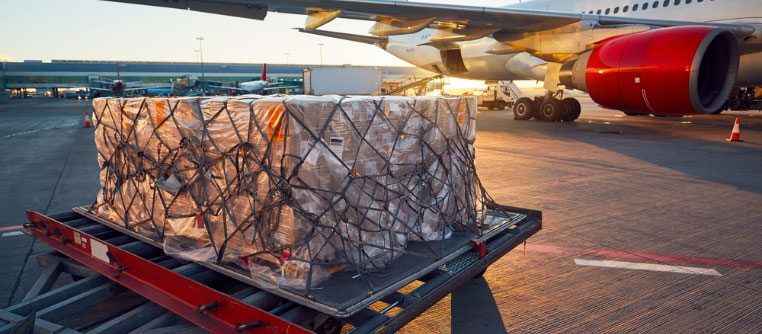
Why is quality important for a business?
Whether you’re big or small, managing quality is a must for every business. Quality is often an important factor and major differentiator in a competitive market.
From retaining customers to maintaining a reputation, there are many reasons why the quality of your products should be your priority.
Customer satisfaction
Customers expect your product to meet their needs and standards. If you sell them a poor-quality product, they will turn to one of your competitors in the future.
Your customers should be able to trust your business to provide high-quality products. This increases your chances of profitability and allows you to maintain higher prices for your goods. Customers generally justify paying a higher price for a better product.
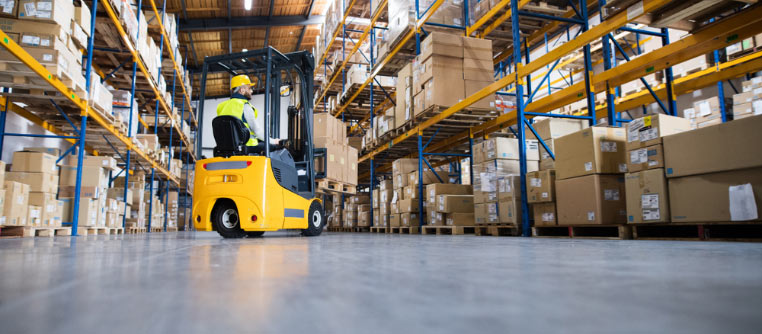
Reputation
More than ever, customers are relying on word-of-mouth recommendations from their peers to determine whether a brand is right for them. If you’re selling poor-quality products, negative reviews and criticism can damage the public perception of your brand.
When your customers are satisfied with the quality of your products, you’re more likely to experience favourable feedback and reviews recommending your brand to prospective customers. A reputation for quality can be the deciding factor between your business and a competitor.
Costs and productivity
Poor-quality products can cost your business time and money:
- Paying for returns and replacements on faulty products
- Costs to analyse and retest goods
- Production costs to replace goods
- Freight costs to pick up defective products and deliver new supply
- Potential legal costs if customers sue
Industry standards
Your customers are not the only ones with expectations for quality. Depending on the type of products you’re selling, you may be required to achieve accreditation with quality standards.
For example, if your company supplies building products, generators, or electrical goods, you’re required to comply with the relevant regulatory bodies standards.
Accredited quality control systems confirm that your business meets industry standards for quality, and can assist your business in appealing to new customers and markets.
And if you’re not meeting these standards, you’re taking on unnecessary risk and potential liability. If someone is injured using your product, you may be held responsible.
Within a supply chain, the cost of poor quality products has a cumulative effect. The compounding effects of product returns, reworking, freight and lost sales can lead to production delays, chargebacks and cancelled orders. The investment in quality is worth it.